Products
- Plant component
- Equipment
- Project
- Service support
New Products
3-Step Pungent Flavor Changeover
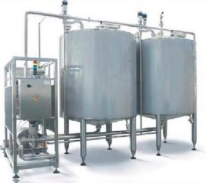
Summary
To prevent flavour and odor cross-contamination in finished beverages, intensive line-cleaning
regimes are required when changing from pungent to non-pungent flavour products. These
cleaning cycles typically required a lengthy hot 3-step or cold 4-step CIP. The duration of these
CIP processes typically average 120 minutes, Trustwater was challenged to test and validate its
innovative rapid ECA changeover protocol with the aim of reducing changeover times and to
provide the plant with a safe alternative to traditional chemicals. The objective was to enable the
plant to increase production and to move towards a ‘Just- In-Time’, lean manufacturing model.
Background
This study was carried out on a US based, 5-line Carbonated Soft Drink bottling plant which
consists of 16 syrup tanks, 2 can lines,3 PET lines and 1 Bag-In-Box line. The plant operates
24/7.This facility runs 800-900 pungent/sensitive changeovers per year.
Approach
Initially, a number of bench-top tests were performed and proved successfully in removing
pungent flavours from beakers and other selected surfaces . Following this initial success, a test
rig was designed to perform dynamic continuous flow tests, simulating typical plant CIP cleaning
conditions, These tested varying contact times, end-user products, dried-on materials and
different substrates. Trustwater subsequently connected a generator and skid platform to the CIP
system. The former 120 minute CIP protocol was replaced with a much shorter 3-step
Trustwater ECA protocol. The total duration of the new Trustwater 3-step pungent flavour
changeover was 20 minutes. In order for the company to approve use of the 3-step changeover,
it was necessary to validate as per the protocol below:
Protocol for Pungent Flavours Changeovers with Trustwater:
1. Clean and sanitize a production line in one step using Trustwater
2. To evaluate production line changeover effectiveness , test and document the following parameters:
Trustwater Concentration | Test Trustwater solution at the filler during wash to ensure concentration level is achieved |
Trustwater Removal | Test final rinse for residual |
Taste, Odor, and Appearance of Final Rinse Water | Perform a taste test on the final rinse water to ensure no off-flavor, odors or colors |
Taste, Odor, and Appearance of Finished Beverage | Perform a taste test on the containers from the first commercial turn of the filler to assure no off-flavours, odors or colours prior to production |
Taste Analysis | For the first two changeovers from a pungent to a non-pungent, submit: Two finished product containers from the first commercial turn of the filler ,and two finished products samples from the end of the run to be used as a control |
Odor Analysis of Rinse Water | For the first two Trustwater ECA CIPs per line: Submit four samples of final rinse water from the filler for odor analysis Send four samples of the final rinse water from a non-Trustwater CIP to be used as a control |
3.Repeat steps 1 and 2 a total of 20 times to collect the required Trustwater changeover data
4.Submit data for Trustwater changeover sanitization approval
Results:
Following the trail and strict validation process it was evident that Trustwater had successfully
developed and implemented the first ECA pungent flavour changeover CIP, reducing individual
CIP times by an enormous 100 minutes.
Plant Benefits:
Pungent flavour changeover reduced from 120 minutes to 20 minutes
Increased production up-time by over 130000 minutes per annum
Labor saving of $242985 per annum
Increased water savings
Significant energy savings
- ·Welcome toSuntyech Process Engineering (Shang Hai) Co.,Ltd.!!!
- ·Welcome toSuntyech Process Engineering (Shang Hai) Co.,Ltd.!!!
- ·Welcome toSuntyech Process Engineering (Shang Hai) Co.,Ltd.!!!
- ·Welcome toSuntyech Process Engineering (Shang Hai) Co.,Ltd.!!!
- ·Welcome toSuntyech Process Engineering (Shang Hai) Co.,Ltd.!!!
- Leave message